静电植绒中电场的模拟与优化
发布时间
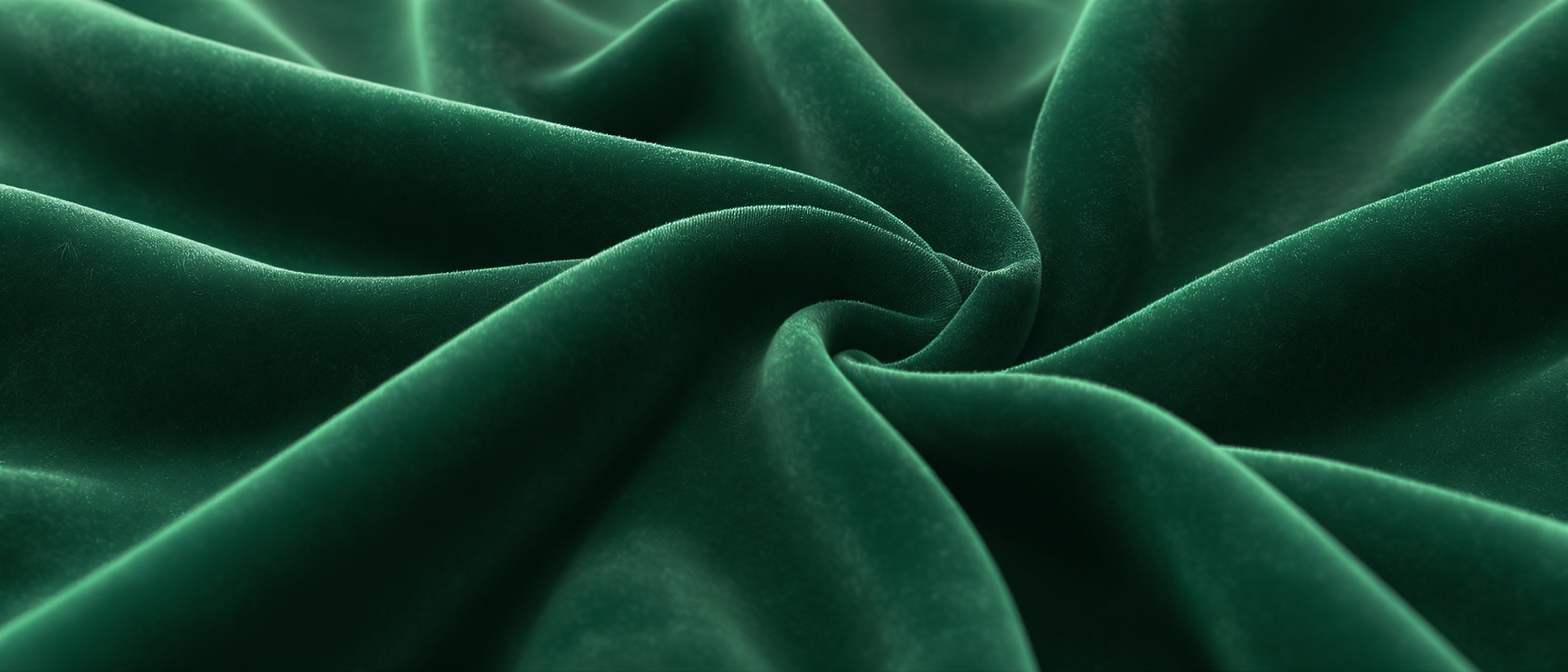
引言与研究背景
静电植绒作为一种利用电荷同性相斥、异性相吸物理特性的生产工艺,通过高压电源构建强电场驱动带负电绒毛有序附着于涂有胶粘剂的基材表面,具有工艺简单、成本低、装饰效果独特(如绒面、刺绣感)等特点,广泛应用于美术装潢、汽车内饰、包装、工艺品、家纺等领域。其核心流程涉及绒毛带电、电场作用、粘合剂固化等多物理过程,是材料表面处理和装饰领域的重要技术。
从物理机制看,静电植绒的核心驱动力是高压电源构建的电场分布。绒毛的定向运动、疏密程度及吸附效率均直接受电场均匀性、稳定性和强度的影响:电场均匀性不足(如电压波动)会导致绒毛疏密不一,尤其在大规模生产植绒壁纸等产品时易引发质量问题;电场稳定性(高压电源输出稳定性)决定了植绒效果的一致性;而电场强度(40-60kV电压范围)则是实现最佳吸附效率的关键参数。绒毛疏密程度进一步影响产品的外观、触感、耐磨性等物理性能,因此电场分布的精准调控是提升植绒质量的核心环节。
然而,当前植绒工艺面临显著挑战:传统静电植绒及喷涂植绒存在效率低下、绒毛浪费严重、环境污染较重等问题,大规模生产中能源消耗和材料损耗尤为突出;同时,因电场分布不均导致的绒毛疏密不一、植绒不牢(如PP等非极性材料表面)等问题,常造成15%-20%的次品率,直接增加生产成本。在此背景下,电场分布的模拟与优化成为解决上述问题的关键技术路径——通过精确模拟电场分布规律,可针对性优化高压电源参数、电极结构及材料介电特性匹配,从而提升绒毛吸附效率和分布均匀性,降低次品率并减少材料损耗
基于此,本报告的核心目标是系统梳理植绒电场分布的模拟方法(如静电场建模、多物理场耦合分析)、优化策略(电场参数调控、电极结构设计、材料特性匹配)及实际应用挑战(复杂形面适配、能耗经济性、环境敏感性),为静电植绒工艺的技术改进和工程应用提供理论支撑与实践参考。
植绒电场分布模拟基础理论体系
静电感应与电荷耦合机制
静电植绒过程中,极板电荷密度与电压的线性关系是理解电场分布的基础。根据电磁学基本原理,极板间电场强度(E)由极板电压(U)与两极间距(d)决定(E=U/d),而极板电荷密度(σ)与电场强度满足线性关系σ=ε₀·E(ε₀为真空介电常数),这一关系揭示了电压对极板电荷分布的直接调控作用。
绒毛的带电过程涉及接触带电与极化带电的耦合机制。绒毛通常通过接触负极(如金属网框)获得负电荷,同时在电场中发生极化:与负极极性相同的负电荷集中于远离负极的一端,正电荷则集中于靠近负极的一端。由于电极材料的电导率显著高于绒毛,最终绒毛表现为携带净负电荷。此过程不仅实现了电荷的接触转移,还通过电场极化进一步强化了电荷积累,是接触带电与极化带电共同作用的结果。
电场分布直接影响绒毛的初始加速度与运动轨迹。带负电的绒毛在电场中受电场力作用产生平动与转动的复合运动:平动表现为变加速运动,其初始加速度与电场强度(由极板电压和间距决定)及绒毛带电量呈正相关,电场强度越高、带电量越大,绒毛初始速度提升越快;转动则为周期性小阻尼振动,振幅随时间逐渐减小,最终稳定在垂直于极板的平衡位置。这种运动特性使得绒毛在电场中伸直并高速垂直运动,最终以直立状态附着于涂胶基材表面。若电场分布不均或强度不足(如电压低于20kV),绒毛竖直性将显著下降;而电场过强(如电压高于100kV)则可能引发静电火花烧毛等问题,进一步验证了电场分布对绒毛运动轨迹的关键调控作用。
数值模拟方法对比与选择
在植绒电场分布模拟中,常用的数值模拟方法主要包括有限元法(FEM)、边界元法(BEM)和有限差分法(FDM)。不同方法在原理、适用场景及计算特性上存在显著差异,需基于具体模拟需求采用“场景适配”策略进行选择。

有限元法(FEM)通过将连续域离散为单元求解麦克斯韦方程组,支持二维(如ELECTRO)和三维(如COULOMB)模拟,可处理静态、时间谐波及完全瞬态电场,适用于复杂几何结构的电磁场分布模拟。其优势在于能够处理非线性、各向异性材料(如高压套管、绝缘子等电力设备),并通过Gmsh四面体网格剖分等技术实现三维算例的高精度模拟,结果可与成熟商业软件对比验证。但需注意,FEM的精度高度依赖网格划分质量,研究表明网格尺寸应≤极板最小特征长度的1/10,以确保对复杂极板结构(如曲面极板)的准确模拟。
边界元法(BEM)通过边界离散化降低计算维数,仅需表面网格而非体网格,适用于无界域或大开放区域的电场模拟(如输电塔绝缘子、横向飞跃法中的开放域电场)及薄层问题(如污染绝缘子)。与FEM相比,BEM可减少未知量数量,尤其在处理辐射、散射等无界域电磁场问题时优势显著,但无法处理非线性或各向异性材料。
有限差分法(FDM)通过网格离散将偏微分方程转化为差分方程组,适用于动态电压调制等动态电磁场模拟场景(如时域有限差分法FDTD对天线设计、光子晶体的动态模拟)。其原理简洁、易编程实现(如通过迭代公式求解电场等位线),但对复杂几何形状适应性较差,且存在收敛速度慢的局限性。
综上,针对植绒电场分布模拟的不同场景,推荐采用“场景适配”选择策略:复杂极板结构(如曲面极板)优先选择FEM以应对几何复杂性;开放域电场(如横向飞跃法)选用BEM以高效处理无界域问题;动态电压调制场景则采用FDM(或FDTD)以满足动态电磁场模拟需求。同时,需特别关注FEM的网格划分质量,建议网格尺寸≤极板最小特征长度的1/10以保障模拟精度。
植绒电场优化关键影响因素与技术策略
电压波动的影响与动态调控
电压作为植绒电场的核心参数,其大小与稳定性直接影响植绒质量。研究表明,电压波动通过改变电场强度,显著影响绒毛飞行速度、植入深度及分布均匀性。实验数据显示,植绒密度与电压变化呈线性关系(Δρ=k·ΔU,k=2.4%/kV),即电压每波动1kV,植绒密度将变化约2.4%。具体而言,电压过低(\<40kV)时,绒毛因飞行速度慢、动能不足,易受空气阻力和重力影响,导致植绒密度不足、绒毛倒伏或植入过浅(结合不牢);电压过高(>60kV)则会使绒毛飞行速度过快,可能因过度分散破坏粘合剂或涂层,同时引发空气电离风险,导致绒毛散乱。电压稳定性同样关键,波动会导致电场强度不稳定,造成植绒疏密不均(如大规模生产植绒壁纸时不同区域效果不一致)。
针对电压波动的调控需求,目前主要采用传统PID控制与智能模糊控制两类技术。传统PID控制成本较低(约3000元),通过闭环反馈(响应时间<10ms)补偿负载变化,可控制纹波系数<1%、电压波动±0.5%以内,但抗干扰能力较弱,对复杂负载变化(如涂层厚度偏差>5μm)的适应性不足。智能模糊控制通过定制开发算法(成本约8000元),可实现更高精度调控(电压波动\<±1kV),并支持0.5秒内修正输出电压(60-100kV可调),尤其适用于负载变化频繁的场景。此外,配合脉冲调制技术可精确控制电荷释放速率,结合IGBT变频模块可降低单位面积能耗22%,进一步优化调控效果。
基于不同应用场景的需求差异,建议采用“场景化”调控方案:对于普通植绒(如常规壁纸、基础工业制品),优先选择成本较低的PID控制,兼顾经济性与基本质量要求;对于高精度场景(如汽车内饰、精密电子元件植绒),则需采用智能模糊控制,以确保绒毛取向整齐、立体感强及均匀性要求。
环境湿度的干扰与补偿技术
环境湿度是影响植绒电场分布及植绒效果的关键因素,其干扰机制与补偿技术需从电荷特性、电场分布及材料性能等多维度分析。
环境湿度的干扰机制
环境湿度对植绒过程的干扰主要体现在以下方面:其一,湿度升高会导致绒毛表面形成水膜,加速电荷流失衰减,同时空气水分增加会中和绒毛表面电荷,显著降低其飞行能力与吸附效果,最终导致植绒稀疏。实验表明,湿度每升高10%,绒毛表面电荷衰减程度加剧,植绒密度偏差可能达25%。其二,湿度变化会改变空气介电常数,直接影响平行极板间的电场分布;当相对湿度>70%时,绝缘介质表面易凝露形成液膜,进一步改变介电性能,加剧电场分布的不均匀性。其三,湿度对胶水性能与绒毛状态亦有显著影响:高湿度会延缓胶水干燥速度并降低粘性,导致植绒牢度下降;而绒毛回潮率低于8%时升飞性差、易残留浮绒,高于8%时则运动速度过快且不规则,引发落绒问题。
湿度干扰的补偿技术
从补偿机制看,水分子的极化弛豫时间约为10⁻⁶s,在高频电场(50-100kHz)作用下,水分子可快速完成极化过程,减少对绒毛表面电荷的中和作用,从而稳定电场分布与绒毛轨迹。
在技术实现上,一方面通过在开放式极板周围增设精度为±2%RH的湿度传感器,实时监测局部微环境湿度;另一方面基于湿度补偿模型,动态调整高压电源输出频率(50-100kHz区间切换),以适应湿度波动。实验验证,该方案可将湿度干扰导致的植绒密度偏差从25%有效降至5%。此外,多物理场仿真技术可进一步优化补偿效果:通过建立液膜厚度-介电常数模型,或利用流体力学软件仿真液膜温湿度分布,为电场补偿策略提供更精准的参数支持。
为保障整体植绒效果,环境湿度需控制在适宜范围(建议40%-60%),当相对湿度>70%时需启动电极除湿模块,避免液膜对电场的额外干扰。
综上,通过结合高频电场补偿机制与局部微环境控制技术,可有效降低环境湿度对植绒电场分布的干扰,提升植绒密度与牢度的稳定性。
极板结构参数优化设计
极板结构参数的优化设计是提升植绒电场均匀性与植绒质量的核心环节,需综合考虑极距、电压与材料特性的协同作用,同时结合动态控制与结构创新策略。
首先,极距与电压是影响电场强度的关键参数,其优化需结合绒毛材料特性构建"极距-电压-材料"三维模型。极距(极板间距)直接影响电场强度,实验表明植绒密度与极距呈反比关系,且存在临界极距(超过该距离时植绒量为零)。实际工艺中,两极间距通常控制在6-10cm(60-100mm),但若极距过大,电场强度减弱会导致绒毛飞行效果下降;极距过小则易引发电场击穿。针对不同绒毛材料(如粘胶、尼龙),极距与电压的敏感性存在差异:尼龙绒毛中,电压对植绒密度的影响大于极距(影响顺序为"纤维长度>极板距离>纤维细度>极板电压");而粘胶绒毛中,极距的影响更显著(影响顺序为"纤维长度>极板电压>极板距离>纤维细度")。基于此,三维优化模型可针对粘胶绒毛给出具体参数建议:极距60-80mm,电压50kV,以平衡电场强度与植绒效果。

其次,极板结构设计是优化电场均匀性的重要手段。传统平板极板的电场均匀性仅为80%,而采用3D打印技术定制的曲面极板(如抛物线型)可将均匀性提升至95%以上,有效改善绒毛带电状态与运动轨迹。此外,极板形状(如网状、栅状或平板状)对绒毛分布有显著影响:网状或栅状上极板(金属网框)可避免绒毛桥络,促进均匀分布并集中飞行方向;平行板状电极因易产生桥络,仅适用于单面加工。针对复杂形面(如汽车内饰多曲面),多级电极阵列系统(16通道独立电压控制,精度±5%)可实现边缘区域电场强度补偿,解决异形件植绒均匀性问题。

最后,动态极板设计方案通过伺服电机与激光测距闭环控制(响应时间20ms),可实时调整极距以适应不同材料或形面需求,进一步提升电场稳定性。该方案结合曲面极板与多级阵列技术,形成从参数优化到动态控制的完整技术链,为植绒工艺的高精度、高均匀性生产提供了有效支撑。
不同植绒工艺的电场适配性分析
植绒工艺的电场适配性需结合工艺类型的绒毛运动方向、设备特性及基材需求进行针对性优化。目前主流植绒工艺按绒毛飞扬方向可分为下降法、上升法、横向飞跃法等类型,其电场分布特点及优化需求存在显著差异,具体分析如下:
1. 下降法:作为国内应用最广的工艺(占比超80%),其采用上极板为金属网框、下极板为金属平板的电极结构,绒毛在降落过程中带电并极化,电场强度由极板电压(U)和极板距离(d)决定。最佳电压范围为40-60kV,电压过低易导致绒毛稀疏,过高则可能破坏粘合剂或涂层。仿真结果显示,下降法边缘电场梯度较大(ΔE=10kV/m),需重点优化极板边缘形状以改善边缘电场分布;此外,绒毛在电场力与重力作用下垂直下落,运动轨迹以变加速平动和小阻尼振动为主,需通过控制电场强度与带电量优化绒毛插入角度,主要适用于平面植绒产品(如壁纸、布匹)。
2. 上升法:绒毛向上运动植入基布,传统工艺存在植绒不均匀问题,改进后通过纱线旋转运动提升均匀度。由于需克服重力影响,其电场强度需求高于下降法(建议电压比下降法高10%),且电压稳定性直接影响植绒均匀度,电流稳定性则关系电荷释放均匀性。绒毛运动轨迹受电场力、重力与空气阻力共同作用,控制复杂度更高,主要适用于高均匀度特殊产品(如纱线植绒)。
3. 横向飞跃法:绒毛横向运动植入基材,需适配横向运动特点设计特殊电极结构与电压参数。由于绒毛水平运动,电场作用时间需延长(建议极板长度增加20%);同时,其运动轨迹易受空气流动、电场不均匀性干扰,需通过精确模拟优化电场分布。该工艺主要适用于横向植绒特殊产品(具体场景待研究)。
三种植绒工艺的电场适配性对比总结如下表:

按设备类型划分,植绒工艺包括流水线式、箱式、喷头式等,其电场参数(如电场强度、作用时间)需适配基底材料特性(导电性、表面形状等)及生产需求。流水线式适用于连续生产(如植绒布、革),需匹配稳定的匀强电场;箱式适用于小尺寸产品,通过箱内高压电场实现快速植绒(3-5秒完成);喷头式通过喷头输出高压静电使绒毛带电,适用于不规则表面植绒。此外,立体植绒(手提式设备适应不规则制件)、静电-风动植绒(电力与风力结合适应复杂形状)、水平电极-机械加料植绒(适应旋转对称制件)等特殊工艺,需通过调整电场参数(电压20-100kV、电流、植绒时间)满足不同绒毛材料(棉纤维、粘胶纤维、尼龙等)和基材(塑料、木材、皮革等)的密度、均匀性及牢固度需求。

针对非极性材料(如TPU、工程塑料、PP塑料),需通过表面等离子处理(电晕值38-42dyn/cm)、导电剂掺杂或PP植绒底涂剂增强极性和粗糙度,并优化静电参数及胶水涂布工艺,可使尼龙、涤纶绒毛在复杂曲面的吸附合格率提升至98.6%。对于复合材料(如碳化棉织物+碳纤维),则可通过电场实现绒毛垂直排列,适配重油清理等特殊场景。
优化效果评估与验证体系
质量与经济性指标
本章节构建"质量-成本"双维度评估模型,系统分析植绒优化过程中质量与经济性的关键指标及评估方法,为优化方案的选择提供量化依据。
质量指标体系
质量指标主要涵盖物理性能、结构特征及外观触感三大维度。物理性能方面,核心指标包括耐磨性能(Taber法测试循环次数≥1.2万次)、抗静电性能(表面电阻≤1×10⁹Ω)及疏水特性(接触角>120°),此类指标直接反映产品的功能性与耐用性,实验数据表明优化后的植绒产品可稳定满足上述要求。结构特征方面,植绒密度(单位面积植绒量或绒毛覆盖面积占比)、均匀性(不同区域绒毛疏密均匀,显微镜观察或光学检测精度±2%)、牢度(绒毛插入粘合剂深度、落绒率,如尼龙/涤纶绒毛在复杂曲面的吸附合格率可提升至98.6%)及直立率(立毛状态)是关键参数,其中植绒密度可通过多元线性回归模型预测,理论值与实测值吻合良好。外观触感方面,绒毛疏密程度直接影响产品外观与触感,优化雾化参数(流量200mL/min时气压0.4-0.6MPa、电压<80kV)可使膜厚标准差从12.3μm降至4.7μm,显著提升均匀性;此外,色差控制需通过统一原材料批次、染料配伍及后处理助剂实现。

经济性指标体系
经济性指标聚焦能耗、成本及环保效益。能耗方面,引入IGBT变频模块和智能电场调控算法可使单位面积能耗降低22%,有效提升能源利用效率。成本方面,静电植绒技术虽存在设备投资大、技术要求高的初始门槛,但高效高压电源支持下的生产效率提升(如减少实验次数、降低能耗)及工艺简化(仅需涂胶、植绒、烘干等步骤)可显著降低长期生产成本;实际案例显示,某壁纸厂改造后年节约成本12万元,投资回收期约0.4年。环保效益方面,相比传统工艺,静电植绒技术通过减少化学溶剂使用实现更环保的生产过程,进一步降低隐性环境成本。

综合评估建议,优化方案应优先选择"质量提升>10%且回收期\<1年"的技术路径,兼顾质量改善的显著性与经济投入的合理性,确保技术优化的可持续性与实际应用价值。
综合验证与迭代优化
植绒电场分布模拟与优化的综合验证及迭代优化过程可通过"模拟-小试-量产"三阶段验证流程实现,各阶段通过数据反馈与技术优化形成闭环,最终保障量产稳定性。
第一阶段:数字孪生模拟验证。该阶段以有限元模拟(FEM)为核心,通过数值模拟与实验对比验证模拟准确性。例如,采用演示仪观察绒毛运动现象、分析纸屑形状对实验现象的影响等方法进行误差分析,确保模拟误差控制在10%以内。进一步地,有限元三维算法通过简单算例(如内导线电位1V、外导线0V,中间介质层)验证,结合Gmsh四面体网格剖分结果与成熟商业软件对比,确认模拟模型的正确性。熔喷静电纺丝模拟中,纤维下落速度与静电力、粘度的关系与实验结果一致,验证了模拟方法的可靠性。通过分析仿真与实验的误差来源并改进模型,可有效提升模拟精度,为后续阶段提供可靠的预演支持。
第二阶段:小批量试产验证。在数字孪生模拟基础上,开展500m²规模的小批量试产,重点验证植绒疏密度与合格率(目标≥98%)。实验验证方法包括正交设计、方差分析(如尼龙/粘胶绒毛影响因素排序差异分析)及多元线性回归模型(理论表达式与实测值拟合良好)(。同时,通过开发新型纱线植绒装置(如旋转砂轮带动纱线旋转)提升均匀度,结合显微镜观察横截面及表面结构对比改进前后效果,并利用烘箱预烘(75-85℃,1.5min)和焙烘工艺固定绒毛,实现初步迭代优化。此外,静电植绒毛绒飞升性能测定仪通过测量毛绒在电场中全部飞起的时间,评估其飞升性能,为质量稳定性验证及生产工艺优化提供数据支撑。集成机器视觉的闭环反馈系统可实时监测植绒密度,进一步保障试产阶段的质量控制。
第三阶段:产线改造与量产优化。基于小试数据,对产线参数进行调整(如极距微调±2mm),最终实现量产稳定性(连续3批次合格率≥99%)。产线改造中,智能控制系统通过实时追踪膜厚等关键参数,与电源模块形成闭环反馈,可在0.5秒内修正参数;同时,通过引进新设备、优化流程等持续改进措施,实现固化温度/时间的精确控制,提升质量稳定性。集成机器视觉的闭环反馈系统结合PID算法动态调整电场参数(如电压、极距),可将产品不良率控制在0.3‰以内。针对PP塑料等材料的植绒不均问题,通过表面预处理与工艺参数调整实现迭代优化。此外,约束驱动优化算法(如遗传算法、粒子群算法)可结合环境约束建模(如风速补偿),通过实验/仿真验证优化效果,进一步提升量产阶段的工艺稳定性。
通过上述三阶段验证流程的协同作用,模拟、试产与量产数据形成有效反馈,推动植绒电场分布优化效果的持续提升,最终实现高稳定性、高合格率的量产目标。
结论与未来展望
现有研究已系统阐明静电植绒的电场作用原理,并通过时域有限差分法(FDM)、有限元法(FEM)和边界元法(BEM)等数值模拟方法,实现了电场分布的多维度分析。实验与模拟验证表明,电场参数(如电压)、环境湿度等对植绒质量具有显著影响,同时基于四旋翼飞行器的节能策略及PP材料表面处理方法等应用技术已取得初步进展。然而,当前研究仍存在显著局限性:模型构建时普遍简化了环境因素(如温度、湿度)的影响,且多聚焦于理论模拟,实际工业生产中的应用验证不足;数值模拟方法(如有限差分法)对复杂几何结构的适应性较差,网格密度与计算效率的矛盾尚未完全解决。
基于上述研究现状与技术瓶颈,结合文献中的发展趋势分析,未来可重点推进以下三个方向的研究:

1. 多物理场耦合模拟优化:当前电场模拟多聚焦于单一电场分析,未充分考虑绒毛运动过程中空气阻力(流场)、焦耳热(热场)等多物理场耦合作用,导致模拟误差较大。未来需整合电场-流场-热场耦合模型,纳入温湿度等环境因素的动态影响,以提升模拟精度(目标误差\<5%)。同时,可通过改进网格划分方法(如非结构化网格、自适应网格)或结合多重网格法,解决复杂几何结构下的计算效率问题。
2. 智能化电场调控系统开发:静电植绒技术正从单一工艺向智能化系统演进,未来需开发基于深度学习的自适应算法,通过积累10万组以上工艺数据(涵盖电场参数、材料特性、环境条件等),实现电场参数的“一键优化”。同时,结合机器视觉实时监测技术,可动态调整高压电源的输出电压与电流(如采用智能控制技术与新型拓扑结构电源),提升电场稳定性与植绒质量。
3. 低介电损耗极板材料研发:现有极板材料的介电损耗较高,导致能耗问题突出。未来需研发陶瓷基复合材料等低介电损耗极板材料,目标降低能耗20%以上。此外,可探索碳纳米管掺杂导电绒毛(导电率提升3个数量级)与100μs级脉冲高压技术的结合,推动传统植绒向高附加值、纳米级精细植绒领域升级。
此外,静电植绒技术的应用领域可进一步拓展,结合喷花、磨花、发泡等工艺开发复合产品,探索纱线植绒等新型应用,同时通过品牌、设计、营销和管理机制创新提升国际竞争力。高压电源技术的持续创新(如新型拓扑结构提高转换效率)与跨领域技术融合(如介质阻挡放电技术结合表面改性),也将为植绒技术的智能化、绿色化发展提供新动力。